Resources - Blog
How Amazon Leverages Artificial Intelligence to Optimize Delivery
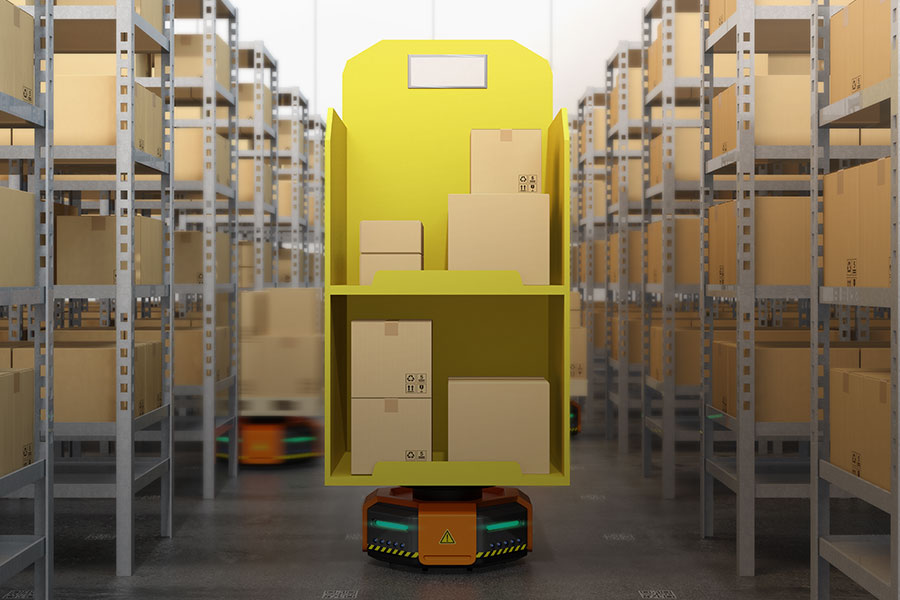
Stay on top of the latest e-commerce and marketplace trends.
At Amazon, artificial intelligence and machine-learning technology are not confined to one business segment. The technology is everywhere, utilized across the teams that back the Alexa suite of voice-activated devices, the Amazon Go stores, and the recommendation engine that cause “Frequently Bought Together” or “Customers Who Bought This Item Also Bought” purchase recommendations to populate.
However, AI-powered technology and deep learning power one of Amazon’s most critical elements of its business — delivery, which is fully dependent on a fluid warehouse operation.
As the U.S. pioneer of one-day shipping, the intricacies of the company’s fulfillment center processes will continue to adapt and evolve to make the end-to-end fulfillment model more streamlined, automated, and sophisticated. In this article, we highlight how Amazon leverages artificial intelligence and machine learning to optimize delivery at scale.
How Amazon Uses AI-Driven Technology Across Its Warehouse Footprint
“Most people look at an Amazon fulfillment center and imagine all the stuff inside. When I look at it, I see data.” -Russell Allgor, Chief Scientist, Amazon Worldwide Operations
With anywhere from 1-4 million product bins per fulfillment center, the Amazon Worldwide Operations team is constantly refining its processes and leveraging technology to determine, in real time, which orders should be picked at the same time to get the products that belong together in the same box.
The team leverages computer vision systems that analyze images to securely track where each item is located throughout the warehouses, which are typically set up with a Manhattan-style grid and have specific, structured paths for the product pods to follow. Each pod has about nine rows of shelves to hold products on all four sides and each warehouse typically ranges between 600,000 to 1 million square feet in size.
Although Amazon says that fully automated shipping warehouses are at least a decade away, robots are currently operating these product pods — in harmony with humans — at 26 of Amazon’s more than 175 fulfillment centers. Spearheaded by Amazon Robotics, which was founded in 2003 as a subsidiary of Amazon.com, fulfillment center automation is backed by technologies including autonomous mobile robots, sophisticated control software, language perception, computer vision, depth sensing, machine learning, object recognition, and semantic understanding of comments.
The company also utilizes artificial intelligence to determine how many units of a specific product it anticipates customers to buy, which then factors into where the product is stocked so it is as close as possible to the people who will buy it.
At Amazon’s re:MARS conference in June 2019, Brad Porter, head of Amazon Robotics, announced two platforms that Amazon has begun integrating into its warehouse operations globally. The first is Pegasus, an item-categorizing system that is predicted to cut down wrongly sorted products by 50%. The other, Xanthus, is a modular drive system that quickly adapts to new applications and attachments that allow it to carry different types of cargo.
With decision engines and decision logic, the technology uses data and information to minimize the distance the pods have to travel at a given time, making decisions constantly as the data on the back end changes. Additionally, the technology builds predictions on how likely a pod may need to be accessed in the next one, two, or three hours. Eventually, a worker will take a specific item from a predetermined station that the robot will travel to and put it on a conveyor belt to prepare it to be shipped.
Once a shipping label is put on the box, the transportation execution processes take over and use machine learning to determine the most effective way the package should travel from point A to point B. The box is sent to a waiting trailer based on its shipping method, speed of delivery, and location. On a daily basis, the team at Amazon uses machine learning and optimization algorithms to improve each warehouse process for one-day shipping, which consumers are already taking advantage of with more than 10 million products.
Final Thoughts
According to Amazon, the integration of robots at fulfillment centers make it possible to store 40% more inventory, which in turn enable it to more rapidly fulfill Prime one- or two-day shipping orders, and more robotics and AI-related innovations will continue to develop and become integrated into Amazon’s global operations model.
Learn what Feedvisor can do for your business.
When you partner with Feedvisor, you automatically receive access to our true, AI-driven technology and hands-on team of e-commerce experts. Contact one of our team members today to learn more about our end-to-end solution for brands and large sellers on Amazon, Walmart, and e-marketplaces.