Resources - Blog
6 Ways to Improve Efficiency, Speed, and Accuracy in Your Warehouse
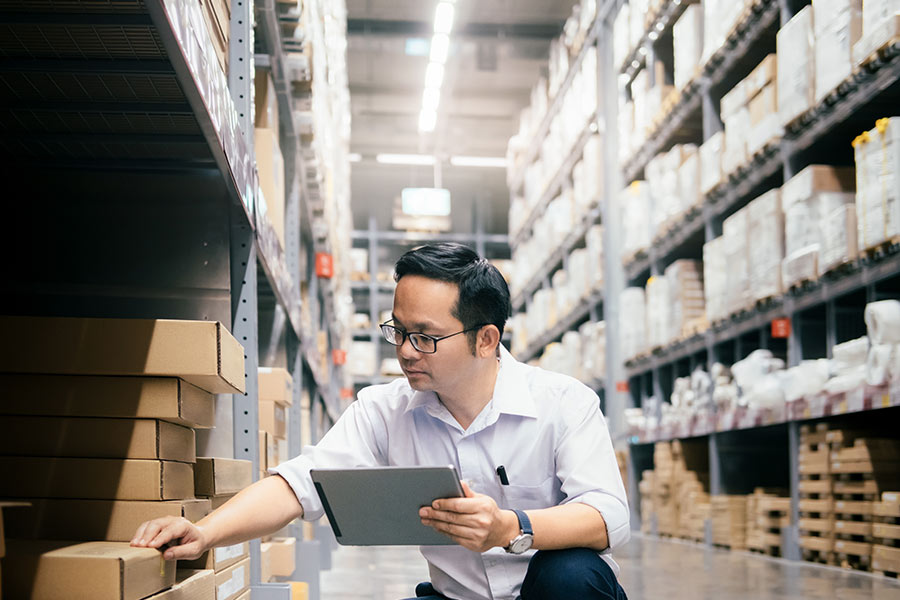
Stay on top of the latest e-commerce and marketplace trends.
The typical U.S. warehouse picks and ships the wrong item between 1-3% of the time, which is a small number that can have a significant impact on your profitability.
On the low end of estimates, a mispicked item may cost you about $30 per incorrect order for shipment and replacement, and you could also potentially lose the customer altogether. The cost of these mistakes scales with your warehouse, so picking 1,000 products a day may cost you at minimum $300, and growing to 5,000 products picked each day brings the cost of mistakes (at the 1% threshold) to $1,500.
When looking at this from a monthly perspective, you are spending tens of thousands of dollars each month solely on errors. There is no better reason than that to focus on optimizing your warehouse processes. The more accurate you are, the lower your error costs. The faster and more efficient you are at the same time, the easier it is to increase your revenue as you control errors.
Get Strategic Around Organization
Your warehouse employees will spend about half their time walking around the floor and picking products. This means they are likely going to be crunched for time with everything else — packing and shipping orders, restocking shelves, putting equipment away, and checking inventory to resupply in time to avoid stockouts.
One of the simplest ways to inject efficiency into your warehouse is to take a look at all of that walking. See where your employees go, what they reach for most, and what makes them perform time-consuming tasks such as return trips or walking to get equipment.
You will be faster and more efficient if you take that data and reorganize your warehouse so that the most frequently picked items are closest to your packing stations. If certain materials always require equipment like a pallet jack or forklift, consider moving products next to your equipment areas to minimize the time they travel between.
Your team is also more accurate when common goods are located near each other because picking orders are more straightforward and there is less room for a mistake.
Check Your Picking Routes
The areas that have your most popular items are going to get busy after you reorganize your warehouse. That grouping is going to increase your productivity, but it can sometimes increase risks to your team. After you make your adjustments, walk the floor and ensure all elements that could be hazardous are taken care of immediately.
Pick up or cover anything that could trip your team (it’s a great time to double check the new floor labeling too) and ensure carts can maneuver around the new layout.
Look for new areas of potential congestion now that space is open. Do not worry if some appear, because the reorganization makes it easy to use batch and wave picking techniques. These have people picking for multiple orders, minimizing task variation and overlap so that they are faster and more efficient.
Establishing clear routes can also help your team stay in the areas they need to be, instead of wandering shelves looking for a product that may have been mislabeled.
Schedule Times for Fast Receiving
Much of the warehouse focus is going to be outbound because that is a significant source of your revenue and where it is easiest to see if you are falling behind and being inefficient. However, you should not forget about inbound manufacturer and vendor shipments.
Having a team ready to receive a shipment when it arrives helps you speed up your dock activities and replenish materials, so you can keep filling orders as fast as you get them. When teams are available, you are also avoiding slowing down the dock and having trailers get stuck, which can sometimes incur charges.
It is generally not possible to always have a team waiting around for a shipment, and it is rarely necessary. Ensure your team is there when you need them by having inbound carriers schedule delivery appointments. You can either give each carrier a specific delivery window or have designated times during the day, week, or month for each carrier.
When your process is optimized and functionality is fine-tuned, you can cross-dock shipments, filling orders with these goods as they arrive.
Train on Communication
The first three elements are all about the action taken in the warehouse. Most warehouse operators realize they will need to train the team on these tactics, whether it is establishing zones for picking, showing crew where equipment should be returned to, or demonstrating how to read an order schedule to know what to do at the dock.
All of that is important to running an efficient warehouse, and it typically requires a strong leader on hand to help remind and reinforce. However, what happens when your floor manager is out sick or stuck in the office?
Your team not only needs to know the actions to take but how to explain and share what’s going on with each other. Communication skills help them assume leadership roles, express what a pick ticket needs, and respond to the support others request. The communication goal is to go from “what do we do?” to “here’s what I’m doing” and “who needs help?”
Adopt a Warehouse Management System
The faster and more elaborate your warehouse, especially with picking routes and methodologies, the more data you are creating and using. Managing it all in Excel can be a significant challenge, especially when you are trying to remove inefficient practices.
Warehouse management systems, or WMS, offer a variety of tools to collect and analyze all of your warehouse information to see what is working and what is not. They can give you statistics on individual employees or products to put people and things in their best position.
One of our favorite WMS features is automatic inventory counts that keep you updated and correct, minimizing downtime for cycle counts and ensuring you do not accidentally run out when demand spikes.
There are plenty of WMS selection checklists available, so look for ones that help you determine the questions to ask vendors as well as features you need and costs to expect.
Find a 3PL Provider to Help
Lastly, if all of the above are getting too cumbersome and you are not sure where to go next, remember that it is okay to ask for help. Third-party logistics providers specialize in getting your goods to your customers with as little fuss and cost as possible. If your warehouse is struggling to get orders out accurately, or you are growing too fast, it might be time to discuss specific services like e-commerce fulfillment.
A reliable 3PL partner can help mid-sized businesses reduce their costs and focus on products and customer service to maximize sales and customer value. Your capital is not tied up in warehousing space, storage, or equipment and maintenance.
In many cases, 3PLs provide cost and accuracy guarantees, so you can properly budget each month and won’t have disappointed customers who are waiting on products or getting the wrong ones. It is one of many ways you can work to improve your overall brand reputation and profitability by tackling warehouse inefficiencies.
Learn what Feedvisor can do for your business.
When you partner with Feedvisor, you automatically receive access to our true, AI-driven technology and hands-on team of e-commerce experts. Contact one of our team members today to learn more about our end-to-end solution for brands and large sellers on Amazon, Walmart, and e-marketplaces.